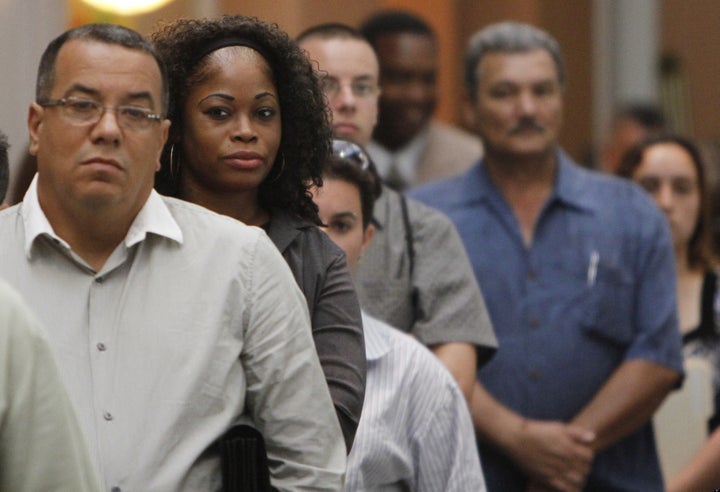
In the sorting out of the wreckage after Japan's earthquake and tsunami, many Americans have begun paying more attention to a phrase they had barely known -- "supply chains."
American manufacturing companies no longer make most of the parts that they use in production. Rather, both U.S. companies and foreign ones that produce for the U.S. market have long and complex chains of suppliers the world over, many of them in Japan. Now, a lot of that production is temporarily idle, while Japan digs out.
The outsourcing of so much production through extensive foreign supply chains, combined with lean and supposedly more efficient "just in time" inventories, leaves companies ranging from Apple to GM vulnerable to supply disruptions half a world away. A few writers such as Barry Lynn and Eamonn Fingleton have been warning about risks of supply-chain fragility for more than a decade, but were paid little attention.
Now, however, we not only have the wake-up call in the form of Japan's earthquake. Economists such as David Levy of the Jerome Levy Forecasting Center, and some dissenting corporate executives such as John Surna of US Steel, point out that it makes less and less economic sense to keep outsourcing production because labor represents a dwindling share of manufacturing costs.
As industry becomes more automated, it takes fewer human workers to manufacture a product. So even if a Chinese worker is paid just one-twentieth the wage of his or her US counterpart, there is only so much that can be saved by moving production abroad.
Almost four decades ago, the Nobel laureate in economics Vassily Leontieff famously imagined a time when machines would be so productive that there would be only one production worker, and her job would be to flip the switch. We are not there yet, but labor cost savings no longer justify the epidemic of outsourcing, given all of the vulnerabilities that it entails.
Meanwhile, as labor costs become less important in manufacturing, energy costs keep increasing. In short, does it really make sense for China to import coal and iron ore from Australia, so that it can fabricate giant wind turbines and send them by ship to the United States? Wouldn't it make more sense for the US to build more of what we consume?
Even in the case of miniature electronics which are less costly to ship, Apple, which designs mostly in the US but out-sources most component production to Asia, could be encouraging more production at home.
As energy and the cost of shipping become expensive, and production becomes more automated, the logic of production shifts back in favor of more domestic manufacturing. However, absent some kind of industrial policy, that will not be sufficient to bring back manufacturing jobs.
Why? Because labor and transportation costs are not the only factors weighing in the decisions of executives of multinational corporations to move production offshore.
Higher environmental and labor standards in the US also make it attractive for multinational companies to outsource production to nations where workers not only have lower wages but no rights, and companies are freer to pollute.
US companies also locate production offshore to take advantage of foreign government subsidies. These subsidies are illegal, in principle, under the World Trade Organization. But China's entire industrial system depends on subsidies intended to attract western companies to shift production to China.
In addition, producing worldwide makes it easier to book profits in such a way that avoids national tax liability. It was recently reported that GE, with worldwide profits of $14.2 billion in 2010, paid no US taxes. In fact, the US ended up owing GE $3.2 billion.
In January, President Obama named GE Chief Executive Jeff Immelt to chair a new presidential council on jobs and competitiveness. But based on GE's record of outsourcing and creative tax avoidance, Immelt should be the poster child for how corporate America ought not to behave.
There is a whole other approach to bringing back manufacturing to the US. Events in Japan and shifting relative prices of labor and energy costs give that approach new compelling logic.
Manufacturing is increasingly hollowed out in the US, but still accounts for upwards of 14 million jobs. It's hard to keep innovating in the US if we lose what's left of our manufacturing industry.
Manufacturing and energy together account for most of our trade deficit, now upwards of $46 billion a month.
As events in Japan remind us, doing more production at home is only prudent. It also makes increasing economic sense. What's missing is more political leadership to put the pieces together.
Robert Kuttner is co-editor of The American Prospect and a senior fellow at Demos. His latest book is A Presidency in Peril.