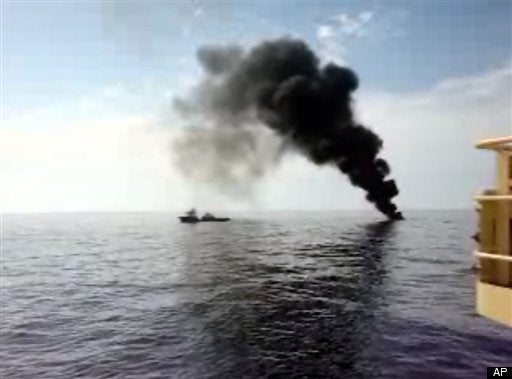
Testimony Before The Committee On Energy & Natural Resources United States Senate May 11, 2010 Outer Continental Shelf Oil and Gas Strategy and Implications of the Deepwater Horizon Rig Explosion Steven Newman, Chief Executive Officer, Transocean, Ltd.
Chairman Bingaman, Ranking Member Murkowski, and other members of the Committee, I want to thank you for the opportunity to speak with you today.
My name is Steven Newman, and I am the Chief Executive Officer of Transocean, Ltd. Transocean is a leading offshore drilling contractor, with more than 18,000 employees worldwide. I am a petroleum engineer by training, I have spent considerable time working on drilling rigs and I have worked at Transocean for more than 15 years. I am proud of the Company's historical contributions to the energy industry during that time. Today, however, I sit before you with a heavy heart.
The last few weeks have been a time of great sadness and reflection for our Company - and for me personally. Nothing is more important to me and to Transocean than the safety of our employees and crew members, and our hearts ache for the widows, parents and children of the 11 crew members - including nine Transocean employees - who died in the Deepwater Horizon explosion. These were exceptional men, and we are committed to doing everything we can to support their families as they struggle to cope with this tragedy.
We have also seen great courage and kindness since April 20 that has reaffirmed our faith in the human spirit. That spirit is embodied by the 115 crew members who were rescued from the Deepwater Horizon and were as worried about the fate of their colleagues as they were about themselves. It is embodied by the emergency workers and friends and family who were waiting for the injured crew members when they arrived ashore. And it is embodied by the friends and colleagues who have rallied to help the families of those who were lost at sea.
While this has been a very emotional period for all of us at Transocean, it has also been a period of intense activity and effort.
Immediately after the explosion, Transocean began working with BP (in BP's role as operator/leaseholder of this well) and the "Unified Command" (which includes officials from the U.S. Coast Guard, the Department of the Interior's Minerals Management Service (MMS), and the National Oceanic and Atmospheric Administration (NOAA)) in the effort to stop the flow of hydrocarbons. Our finest operational personnel and engineers have been working with BP to identify and pursue options for stopping the flow as soon as possible. Our drilling rig, the Development Driller III, is involved in drilling the relief well at the site, and our drillship, the Discoverer Enterprise, is involved in the unique oil recovery operations in the Gulf. We will continue to support BP and the Unified Command in all of these efforts.
We have also been working hard to get to the bottom of the question to which the Members of this Committee - and the American people - want and deserve an answer: What happened the night of April 20th, and how do we assure the American public that it will not happen again?
Transocean has assembled an investigative team to determine what led to these tragic events - a team that includes dedicated Transocean and industry experts. They will be interviewing people who have potentially helpful information and studying the operations and the equipment involved. Our team is working side by side with others, including BP and governmental agencies, and these investigative efforts will continue until we have satisfactory answers.
As is often the case after a tragedy of this kind, there has been a lot of speculation about the root cause. I believe it is premature to reach definitive conclusions about what caused the April 20th explosion, but on behalf of our Transocean employees, I feel compelled to respond to some of this speculation. In particular, as we seek to uncover what happened, it is important to understand the well construction process - and the roles of the various parties involved in an operation like the one that was taking place in the Gulf of Mexico.
All offshore oil and gas production projects begin and end with the Operator. When the Operator (in this case, BP) leases a parcel of land on the outer continental shelf (OCS) from the U.S. government, it must prepare and submit detailed plans specifying where and how a well is to be drilled, cased, cemented and completed based on its interpretation of propriety data, including geologic data from seismic surveys. Once those plans are approved and permits are issued and work begins, the Operator - or leaseholder - serves as the general contractor that manages all of the work that is performed on its lease. In this capacity, the
Operator hires various contractors to perform specific functions in the construction of the well.
In addition, the Operator brings in various sub-contractors to perform specific roles. For example:
- The Operator selects a driller (in this case, Transocean), which provides a vessel (called a "rig") from which drilling operations are performed. As the name suggests, the driller is also responsible for rotating the long string of drill pipe with a drill bit on the end that drills a hole deeper and deeper into the ocean floor. The Operator's well plan dictates the manner in which the drilling is to occur, including the location, the path, the depth, the process and the testing. The drill bits, which are selected by the Operator, are supplied by another sub-contractor.
- A key element of the drilling process is drilling mud, a heavy fluid manufactured to the Operator's specifications. That mud is pumped into the well hole and circulated in order to hold back the pressure of the reservoir and prevent oil, gas or water in that reservoir from moving to the surface through the well. The mud is monitored by another sub-contractor (the mud engineer) (in this instance, M-I Swaco) to detect any problems.
- As the drilling progresses, huge pipes are inserted into the well to maintain the integrity of the hole that has been drilled and to serve as the primary barrier against fluids entering the well. This job is coordinated by the casing sub-contractor selected by the Operator (in this case, Weatherford). In its well plan, the Operator specifies the diameter and strength of each casing segment, purchases the casing, and dictates how it will be cemented in place. Well casing is inserted in a telescope-like manner, with each successive section inside the previous one. Each casing segment also includes a seal assembly to ensure pressure containment.
- After drilling is concluded, yet another area of expertise comes into play. The cementing sub-contractor is responsible for encasing the well in cement, for putting a temporary cement plug in the top of the well, and for ensuring the integrity of the cement. The purpose of this work is to seal the well to make sure that the contents of the reservoir (i.e., oil and natural gas) are not driven by the reservoir pressure into the well. (Once drilling is complete and the well is cased and cemented, it is no longer necessary to circulate drilling mud through the well; at that point, the casing and cement serve to control the formation pressure.) The cementing process is dictated by the Operator's well plan, and the testing of the cement on the Deepwater Horizon was performed by the cement contractor (Haliburton in this instance) as specified and directed by BP.
Against that background, let me turn to the April 20 Deepwater Horizon explosion and its possible causes. What is most unusual about the explosion in this case is that it occurred after the well construction process was essentially finished. Drilling had been completed on April 17, and the well had been sealed with cement (to be reopened by the Operator at a later date if the Operator chose to put the well into production). At this point, drilling mud was no longer being used as a means of reservoir pressure containment; the cement and the casing were the barriers controlling pressure from the reservoir. Indeed, at the time of the explosion, the rig crew, at the direction of the Operator, was in the process of displacing drilling mud and replacing it with sea water.
For that reason, the one thing we know with certainty is that on the evening of April 20, there was a sudden, catastrophic failure of the cement, the casing, or both. Therein lies the root cause of this occurrence; without a disastrous failure of one of those elements, the explosion could not have occurred. It is also clear that the drill crew had very little (if any) time to react. The explosions were almost instantaneous.
What caused that catastrophic, sudden and violent failure? Was the well properly designed? Was the well properly cemented? Were there problems with the well casing? Were all appropriate tests run on the cement and casings? These are some of the critical questions that need to be answered in the coming weeks and months.
Over the past several days, some have suggested that the blowout preventers (or BOPs) used on this project were the cause of the accident. That simply makes no sense. A BOP is a large piece of equipment positioned on top of a wellhead to provide pressure control. As explained in more detail in the attachment to my testimony, BOPs are designed to quickly shut off the flow of oil or natural gas by squeezing, crushing or shearing the pipe in the event of a "kick" or "blowout" - a sudden, unexpected release of pressure from within the well that can occur during drilling.
The attention now being given to the BOPs in this case is somewhat ironic because at the time of the explosion, the drilling process was complete. The well had been sealed with casing and cement, and within a few days, the BOPs would have been removed. At this point, the well barriers - the cementing and the casing - were responsible for controlling any pressure from the reservoir.
To be sure, BOPs are an important aspect of well control. During drilling, BOPs provide a secondary means of controlling pressure if the primary mechanisms (e.g., drilling mud) prove inadequate. BOPs are robust, sophisticated pieces of equipment that can be activated by various direct and remote methods. Since the BOPs were still in place in this circumstance, they may have been activated during this event and may have restricted the flow to some extent. At this point, we cannot be certain. But we have no reason to believe that they were not operational - they were jointly tested by BP and Transocean personnel as specified on April 10 and 17 and found to be functional. We also do not know whether the BOPs were damaged by the surge that emanated from the well beneath or whether the surge may have blown debris (e.g., cement, casing) into the BOPs, thereby preventing them from squeezing, crushing or shearing the pipe.
For these reasons, I believe it is inappropriate to focus any causation discussions exclusively on the BOPs. Certainly, we need to understand what happened to the BOPs and whether changes should be made to improve the effectiveness of these devices in the unusual circumstances of an accident like the one on April 20. But the BOPs were clearly not the root cause of the explosion. Our most important task is to understand why a cased and cemented wellbore suddenly and catastrophically failed. As a starting point, our investigative team has looked at numerous possible causes, contributing factors, or trigger events, in an effort to ensure that nothing is overlooked in this investigation.
As I explained earlier, the well construction process is a collaborative effort. For the same reason, the process of understanding what led to the April 20 explosion and how to prevent such an accident in the future must also be collaborative. Ours is an industry that must put safety first. And I can assure you that Transocean has never - and will never - compromise on safety. In 2009, Transocean recorded its best ever Total Recordable Incident Rate (TRIR). And the federal agency charged with enforcing safety on deepwater oil rigs, MMS, which - as you know - is a unit of the U.S. Department of the Interior, awarded one of its top prizes for safety to Transocean in 2009. The MMS SAFE Award recognizes "exemplary performance by Outer Continental Shelf (OCS) oil and gas operators and contractors." In the words of MMS, this award "highlights to the public that companies can conduct offshore oil and gas activities safely and in a pollution-free manner, even though such activities are complex and carry a significant element of risk." In awarding this prize to Transocean, MMS credited the Company's "outstanding drilling operations" and a "perfect performance period."
Despite a strong safety record, Transocean has never been complacent about safety. We believe that any incident is one too many. Last year, our Company experienced an employee accident record that I found unacceptable. As a result, I recommended to our Board of Directors that they withhold bonuses for all executives in order to make clear that achieving stronger safety performance was a basic expectation - and fundamental to our success. That recommendation was accepted, and our Company paid no executive bonuses last year, in order to send a loud message that we evaluate our success in large part based on the safety of our operations.
Until we fully understand what happened on April 20, we cannot determine with certainty how best to prevent such tragedies in the future. But I am committed - for the sake of the men who lost their lives on April 20, for the sake of their loved ones, for the sake of all the hard-working people who work on Transocean rigs around the world, and for the sake of people in each of the affected states and worldwide who rely on our oceans and waterways for their livelihood - to work with others in the industry, with Congress and with all involved federal agencies to make sure that such an incident never happens again.